Transfer Pricing in the context of manufacturing operations “Cost plus” is the beginning, not the end
“TP” is the commonly used abbreviation for Transfer Pricing: the art of finding prices for intragroup transactions that are acceptable for tax purposes. Overriding principle is the ‘arm’s length principle’: a common shareholder or other form of common control should not influence pricing between related parties.
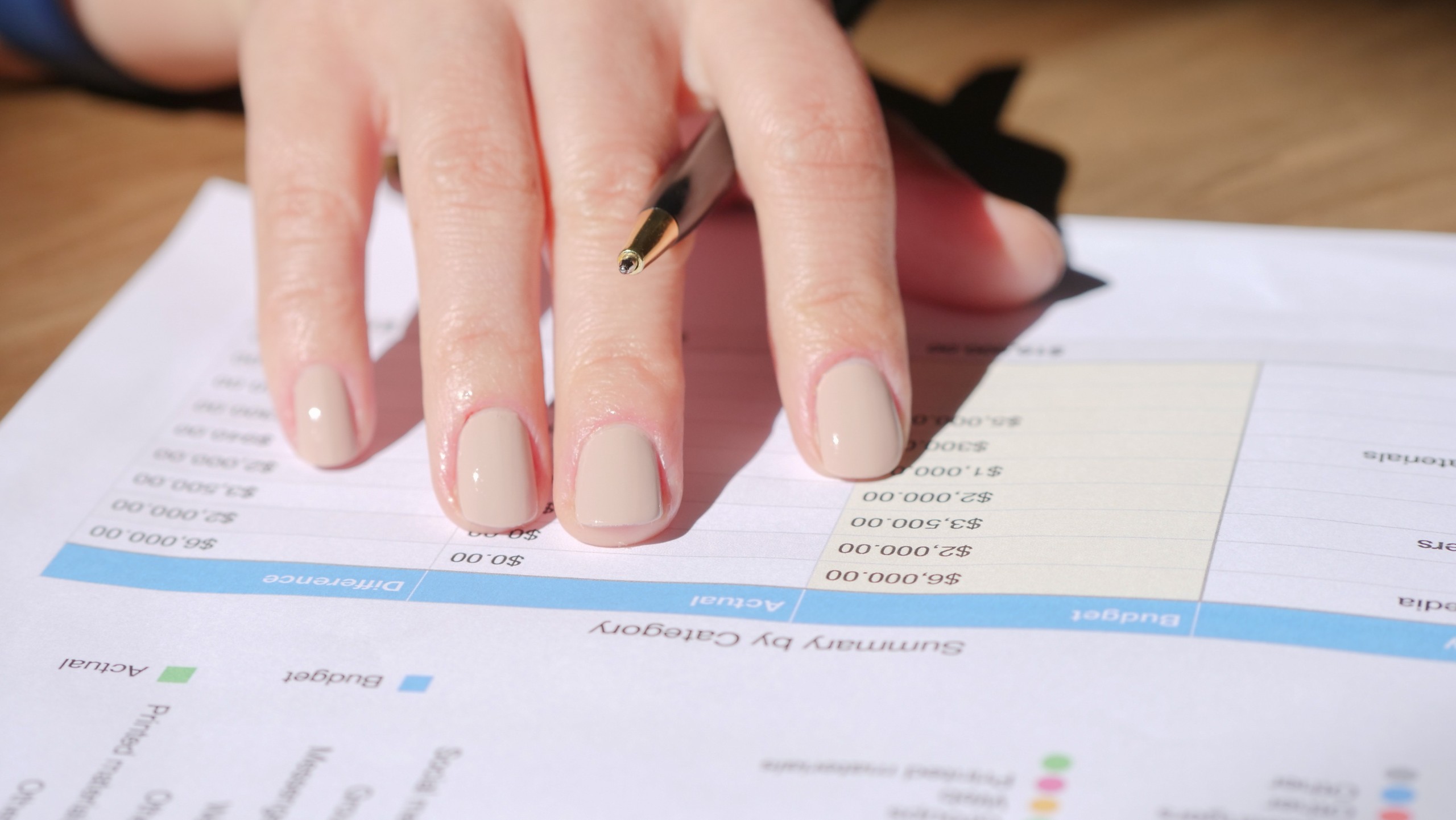
If the terms and conditions, including the pricing, are similar to what independent parties would have agreed upon under similar circumstances, then these prices should be acceptable for tax purposes.
The intragroup sale of goods by a manufacturing entity is a common transaction within groups. When asked how the manufacturing function is remunerated and/or how the goods are priced, in the vast majority of cases the answer given by the business community will simply be ‘cost plus’.
In this article, we will give some context to this ‘cost plus’ in manufacturing environments. The intention is to illustrate that – indeed – the pricing is often based on a certain cost base with an added mark-up. By giving context, we hope to enrich the perception of the term ‘cost plus’ with some of the underlying principles and attention points.
The method
In many cases where a cost-based approach is used in a manufacturing environment, the method is a Transactional Net Margin Method or “TNMM” (the US equivalent of the TNMM is the so-called Comparable Profits Method, often abbreviated to “CPM”). This can be confusing because the expectation may be that the TP documentation mentions “Cost Plus” as the method. Adding to the potential confusion is the fact that there is actually a method called “Cost Plus”, but it is used less regularly in our experience.
In short, without going through all the details of both methods because that is beyond the scope of this article, the TNMM focuses on EBIT (taking into account the full cost base) whereas the ‘real’ Cost Plus method analyses the gross margin and typically does not take into account OPEX and/or indirect manufacturing cost.
By giving context, we hope to enrich the perception of the term ‘cost plus’ with some of the underlying principles and attention points
To verify whether a reference to ‘cost plus’ during a call or meeting relates to a “TNMM” or the actual “Cost Plus Method”, one could ask whether the company is analyzing its gross margin or EBIT. That will likely answer the question.
In the next paragraphs we will assume that a manufacturing entity is remunerated based on the TNMM, whereby a mark-up is added to its total cost base (except financials and extraordinary items). We will refer to this as a ‘cost plus’. For example: if its total operating cost is EUR 1,000,000 and the applicable mark-up is 5%, then it would sell intragroup for EUR 1,050,000 realizing an EBIT of EUR 50,000 which is 5% of total operating cost.
Financial operations
The cost plus is commonly applied and acceptable in most countries. Still, the method can have effects that are counterintuitive. Higher costs imply a higher profit (from an isolated local manufacturing profitability perspective, giving all factory personnel an expensive leasing car could therefore be worth considering). Conversely, if an entity reduces its cost significantly this will lead to a lower profit.
As a result, multinational groups (for internal cost control purposes) and tax authorities (for tax purposes) tend to focus quite heavily on monitoring and controlling the budgeting process to ensure that the cost base is realistic. Also, where actual financial results deviate from the forecasted or budgeted results, it is important to review whether that is the result of local (in)efficiencies that should then be allocated to the manufacturing entity. If the deviation is the result of factors outside the scope of management / control of the manufacturer, the financial impact should be allocated to another group company that managed these risks.
Procurement of group services
Many manufacturing entities receive services from a corporate headquarter, shared service center, IT company, management company or other intra group service providers.
The invoicing of such services to a manufacturing entity remunerated with a cost plus is an attention point (the transfer pricing relating to such services is not discussed in this article, but in most cases service charges are based on a cost-based approach such as the TNMM). Why? The incoming service charges would be reported above the EBIT line in the P&L of the manufacturing entity. That implies that these costs would be included in the cost base of the manufacturing entity and these costs would be marked-up.
There is no true consensus on the best approach here. On the one hand, it can be argued that if the manufacturing entity had procured similar services from an external provider it is clear that these fees would be part of the cost base. On the other hand, it does not seem appropriate that the manufacturing entity receives a mark-up / remuneration for being the recipient of a group service, where the value was added by the service provider.
In practice, there are groups that choose not to invoice manufacturing entities remunerated with a cost plus for intragroup services received. If that decision is made, attention should be paid to other non-TP implications (e.g. cost allocation for management purposes, VAT compliance, etc). If the alternative approach is chosen, i.e. to charge service fees to such manufacturing entities, it is advisable to ensure that no mark-up is applied by the manufacturer to the service fee. This avoids the phenomenon of ‘mark-up over mark-up’ which is often considered inappropriate.
The invoicing of group services to a manufacturing entity with a cost plus (TNMM) type of remuneration is an attention point. Why? The cost of these service charges would likely be part of the cost base and therefore effectively borne by the principal
Final considerations
The cost plus is an appropriate way to remunerate manufacturing activities and it is attractive because of its simplicity. We hope that this article has given the reader some background to the term and its underlying principles and attention points.
In case of further queries regarding this subject, feel free to contact dirk.brouwers@red.tax.